SOP for Sampling and Release of In process Samples.
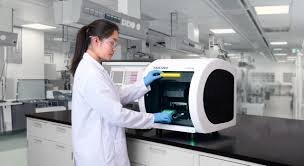
Standard Operating Procedure (SOP)
Here is a Standard Operating Procedure (SOP) for Sampling and Release of In-Process Samples. This SOP outlines the process for properly sampling and releasing in-process samples to ensure quality control during production.
1. Purpose
To provide guidelines for the proper collection, handling, and release of in-process samples during production, ensuring that they meet quality standards before proceeding to the next production stage.
2. Scope
This SOP applies to all personnel involved in the sampling and release of in-process samples in [Company/Facility Name], specifically for [e.g., pharmaceutical, food manufacturing, or chemical production].
3. Responsibilities
-
Production Personnel: Responsible for obtaining in-process samples at designated stages.
-
Quality Control (QC) Personnel: Responsible for receiving, testing, and releasing in-process samples.
-
Supervisor: Ensures compliance with the SOP, monitors the sampling process, and reviews release reports.
4. Materials and Equipment
-
Clean sampling tools (e.g., scoop, spatula, sterile containers)
-
Sample containers (properly labeled)
-
Personal protective equipment (PPE): gloves, lab coat, safety glasses, etc.
-
Sampling instructions/checklist
-
Labels for sample identification
-
Documentation forms (Sampling Log, Release Form)
-
In-process batch records
-
Analytical equipment for QC testing
5. Procedure
5.1 Sampling of In-Process Materials
-
Preparation:
-
Ensure that all sampling tools and containers are clean and sterile (if required).
-
Verify that the sample container is appropriately labeled with relevant information (e.g., product batch number, sample ID, date, time, and operator name).
-
Wear necessary PPE (e.g., gloves, mask, lab coat).
-
-
Sampling Points:
-
Sampling must be carried out at designated points in the production process, as specified in the product’s production batch record or sampling plan.
-
Common sampling points may include during mixing, after filtration, before packaging, etc.
-
-
Collection of Sample:
-
Collect the sample in a manner that avoids contamination.
-
Use appropriate tools for the sample collection (e.g., sterile scoops for powders, pipettes for liquids).
-
Ensure that the sample size corresponds to the specified amount in the SOP or batch record.
-
Avoid overfilling the sample container to allow for any necessary testing.
-
-
Documentation of Sampling:
-
Record the sample collection details in the Sampling Logbook or Batch Record, including:
-
Sample ID
-
Date and time of sampling
-
Sampling point or stage in the process
-
Operator’s name
-
Any notable observations or deviations.
-
-
5.2 Handling and Transport of Samples
-
Proper Storage:
-
If the sample needs to be transported to the QC lab, ensure it is stored under the required conditions (e.g., temperature-controlled).
-
Secure the sample container to avoid spills or contamination during transportation.
-
-
Transporting to QC:
-
Ensure that the sample is transported promptly to the QC laboratory.
-
Maintain sample integrity by ensuring that no exposure to unfavorable conditions occurs (e.g., high temperatures, humidity).
-
5.3 Quality Control Testing
-
QC Receipt of Sample:
-
Upon receiving the sample, the QC analyst will verify the sample label for accuracy.
-
Confirm that the sample matches the specified in-process stage (as indicated in the batch record).
-
-
Testing and Analysis:
-
The QC team will test the sample following the relevant analysis methods and quality control specifications (e.g., pH, viscosity, moisture content, etc.).
-
If needed, follow the detailed testing protocol provided in the SOP for the product type.
-
-
Recording Results:
-
All test results must be recorded in the appropriate format (e.g., result sheets, electronic system).
-
Any deviations or out-of-specification results must be documented, and appropriate corrective actions must be initiated.
-
5.4 Release of In-Process Samples
-
Approval for Release:
-
Once QC testing is completed and results meet the established specifications, the sample may be approved for release to the next phase of production.
-
If the sample passes, the QC supervisor will release the sample and document the release in the Sample Release Form.
-
-
Non-Compliance or Failure:
-
If the sample fails the required tests, a thorough investigation should be conducted to determine the cause of the failure.
-
The in-process material should not proceed to the next phase of production until corrective actions are taken.
-
-
Release Documentation:
-
Ensure all relevant documentation (e.g., release forms, test results) is signed and dated by the QC supervisor and/or manager.
-
Record the release decision in the batch records for traceability.
-
6. Precautions
-
Always ensure that sampling tools are clean and, if required, sterile to prevent contamination.
-
Do not overfill sample containers, as this may affect the quality of the sample or subsequent testing.
-
Always use the correct sampling point as specified in the batch record.
-
Handle samples with care to prevent cross-contamination or exposure to adverse conditions.
-
Adhere to all safety and regulatory guidelines during sampling and handling.
7. Documentation and Records
-
Sampling Log: Maintain a record of all samples taken, including sample ID, time, date, and sampling location.
-
Batch Record: Ensure that all relevant sampling information is recorded in the batch record for traceability.
-
Sample Release Form: Document the decision to release the sample or its failure, along with any corrective actions taken.
-
Test Results: Ensure that the results of QC testing are recorded and filed appropriately.
8. Reference Documents
-
Batch production record
-
In-process specifications for the product
-
Relevant SOPs for testing and analysis methods
-
Equipment calibration and maintenance records
🎓 Discover one of the best Quality Assurance courses available — click below to explore the course that’s shaping future QA skills.