SOP for Trend Analysis.
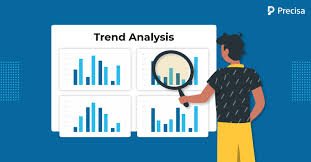
Standard Operating Procedure (SOP)
Here’s a detailed Standard Operating Procedure (SOP) for Trend Analysis. This version is general and can be applied to areas like quality control, production performance, laboratory data, or any context where identifying patterns over time is important.
1. Purpose
To establish a systematic approach for performing trend analysis on relevant data sets to identify patterns, deviations, and potential areas for improvement.
2. Scope
This SOP applies to all departments responsible for monitoring and evaluating data trends, including but not limited to quality assurance, production, and laboratory services.
3. Responsibilities
-
Data Analyst/Responsible Personnel: Conducts the analysis and interprets results.
-
Department Head: Reviews findings and initiates actions based on trends.
-
Quality Assurance: Ensures compliance with data integrity and reporting standards.
4. Definitions
-
Trend Analysis: The practice of collecting data and attempting to spot a pattern.
-
Outlier: A data point that differs significantly from other observations.
-
CAPA: Corrective and Preventive Action.
5. Materials and Tools
-
Data collection systems (e.g., LIMS, ERP, spreadsheets)
-
Statistical analysis software (e.g., Excel, Minitab, R)
-
Charts and graphing tools
-
SOPs for data entry and reporting
6. Procedure
6.1 Data Collection
-
Identify the data set to be analyzed (e.g., product quality, equipment performance, lab test results).
-
Ensure data is complete, accurate, and consistent.
-
Extract data from validated systems or reports over the relevant time period.
6.2 Data Organization
-
Arrange data chronologically.
-
Clean the data to remove duplicate or erroneous entries.
-
Categorize data if needed (e.g., by product, date, shift, equipment).
6.3 Trend Identification
-
Use graphical tools (e.g., line charts, control charts, histograms) to visualize data.
-
Apply statistical tools to identify significant patterns, shifts, or cycles.
-
Compare results to predefined thresholds or specifications.
6.4 Interpretation and Evaluation
-
Determine if a trend is within acceptable limits or indicates potential issues.
-
Identify root causes for abnormal trends or outliers if necessary.
-
Document findings, including possible contributing factors.
6.5 Reporting
-
Summarize results in a trend analysis report.
-
Include:
-
Objective and data reviewed
-
Graphs and statistical outputs
-
Observations and conclusions
-
Recommendations (if applicable)
-
-
Share report with relevant stakeholders (QA, Production, Management).
6.6 Follow-Up and Action
-
If a negative trend is identified, initiate CAPA as required.
-
Track and monitor the implementation and effectiveness of actions taken.
-
Re-analyze data periodically to confirm trend improvement.
7. Frequency
-
Routine trend analyses should be conducted monthly or quarterly depending on the process.
-
Ad-hoc analyses may be initiated after deviations or out-of-spec results.
8. Documentation and Records
-
Trend analysis reports
-
CAPA records (if applicable)
-
Meeting minutes or communications related to the analysis
9. References
-
Relevant SOPs for data entry and handling
-
Statistical guidelines and control chart standards (e.g., ICH Q10, ISO standards)
-
Quality Manual or QMS Guidelines.
🎓 Discover one of the best Quality Assurance courses available — click below to explore the course that’s shaping future QA skills.