SOP for Planning for Analysis and Reporting of Results.
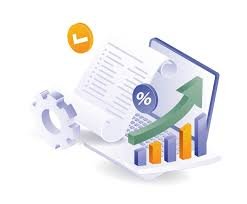
Standard Operating Procedure (SOP)
Here is a Standard Operating Procedure (SOP) for Planning for Analysis and Reporting of Results. This SOP outlines the steps required to plan, analyze, and report results systematically and accurately in a laboratory or quality control setting.
1. Purpose
To provide a standardized approach for planning the analysis and reporting of results to ensure accurate, reliable, and consistent reporting of laboratory or quality control (QC) findings.
2. Scope
This SOP applies to all personnel involved in the analysis, interpretation, and reporting of results within the [Department/Facility Name].
3. Responsibilities
-
Laboratory Personnel/Analysts: To perform analyses, record results, and report in compliance with the SOP.
-
QC Supervisor/Manager: To review and verify analytical reports, ensuring compliance with standards.
-
Documentation Personnel: To ensure proper documentation and archiving of analysis reports.
4. Materials and Equipment
-
Laboratory notebooks or electronic systems for data recording
-
Analytical instruments (e.g., HPLC, GC, spectrophotometer, etc.)
-
Standard Operating Procedures (SOPs) for analytical methods
-
Data analysis software or tools (e.g., Excel, LIMS system)
-
Reports, templates, and forms for documentation
-
Sample containers, reagents, and standards
5. Procedure
5.1 Planning for Analysis
-
Define Objectives:
-
Clearly understand the purpose of the analysis (e.g., routine quality control, method validation, product release).
-
Identify the type of analysis required (e.g., chemical, microbiological, physical testing).
-
-
Preparation of Samples:
-
Ensure samples are collected and labeled appropriately.
-
Check that the samples meet the required storage conditions (e.g., temperature, light, etc.).
-
Verify the proper sample size and volume required for testing.
-
-
Select the Analytical Method:
-
Choose the most appropriate and validated analytical method (e.g., HPLC, titration, spectrophotometry).
-
Review the relevant SOP for the analytical method to ensure proper procedures are followed.
-
Ensure that all necessary reagents, standards, and equipment are available and calibrated.
-
-
Establish Timeline:
-
Define the expected timeline for completing the analysis.
-
Allocate sufficient time for result analysis, calculations, and report generation.
-
-
Preparation of Equipment:
-
Ensure that all equipment is properly calibrated and in good working order.
-
Perform any necessary preventive maintenance before starting the analysis.
-
5.2 Performing the Analysis
-
Sample Analysis:
-
Conduct the analysis following the SOP for the specific analytical method.
-
Ensure that proper precautions are taken to avoid contamination or errors during testing.
-
Record all raw data, calculations, and observations accurately.
-
-
Quality Control:
-
Follow the required QC procedures (e.g., running controls, blanks, or standards) to validate the results.
-
Ensure that any deviations or out-of-spec results are flagged and documented.
-
-
Data Interpretation:
-
Evaluate the data according to established protocols.
-
If necessary, perform calculations, statistical analyses, and comparisons with acceptance criteria.
-
5.3 Reporting of Results
-
Result Compilation:
-
Compile the results from the analysis and document them in the appropriate format (e.g., report, data sheet).
-
Include all necessary calculations, units of measurement, and raw data (if applicable).
-
-
Verify Results:
-
Double-check the accuracy of recorded data and calculations.
-
Verify that results align with the expected criteria, including limits or specifications.
-
-
Prepare Report:
-
Create a final analysis report that includes:
-
Objective of the analysis
-
Sample information (e.g., source, batch number)
-
Analytical method(s) used
-
Results and interpretation
-
Any deviations or issues encountered during testing
-
Conclusions or recommendations (if applicable).
-
-
Ensure that the report is clear, concise, and free from errors.
-
-
Review and Approval:
-
Submit the report for review by the QC Supervisor or designated approver.
-
Review any feedback and make necessary revisions.
-
Once approved, finalize the report for record-keeping.
-
-
Documentation:
-
Ensure that all analysis results, raw data, and reports are properly documented and archived as per company guidelines.
-
Maintain electronic or hard copy records for traceability and audit purposes.
-
6. Precautions
-
Always ensure that the analytical methods are validated and approved for use.
-
Avoid contamination during sample preparation and analysis.
-
Follow all safety procedures when handling reagents and chemicals.
-
Ensure equipment is properly calibrated before use.
-
Ensure that only authorized personnel perform data analysis and reporting.
7. Documentation and Records
-
Analysis Logbook: Record all data and observations during the analysis.
-
Reports: Maintain a copy of the final report in both hard and electronic formats.
-
Review/Approval Log: Maintain a log for approvals and reviews of results and reports.
8. Reference Documents
-
Analytical Methods SOPs
-
Equipment Calibration SOPs
-
Data Management SOPs
-
Quality Control Guidelines
🎓 Discover one of the best Quality Assurance courses available — click below to explore the course that’s shaping future QA skills.