SOP for Cleaning of S.S. Bins, Containers, Pallet, Hosepipes Material Transfer Pipe and Accessories
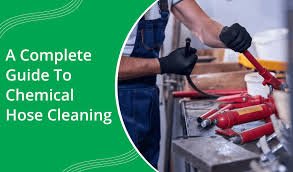
Standard Operating Procedure (SOP)
Here is a comprehensive Standard Operating Procedure (SOP) for the Cleaning of Stainless Steel (S.S.) Bins, Containers, Pallets, Hosepipes, Material Transfer Pipes, and Accessories, commonly used in pharmaceutical manufacturing for material handling and transfer.
1. Purpose
To define the procedure for cleaning and maintaining stainless steel bins, containers, pallets, hosepipes, material transfer pipes, and other accessories to prevent cross-contamination and maintain cGMP standards.
2. Scope
This SOP applies to all S.S. equipment and accessories used for material storage, handling, and transfer in the manufacturing area.
3. Responsibility
-
Operators: Perform cleaning as per this SOP and maintain records.
-
Production Supervisor: Ensure compliance and verify cleaning.
-
QA/QC: Review and approve cleaning activities.
4. Materials and Equipment Required
Approved detergent/disinfectant
-
Purified water
-
Clean lint-free cloths
-
Brushes (non-metallic, dedicated)
-
Cleaning logbook
-
Personal Protective Equipment (PPE)
5. Procedure
5.1 Pre-Cleaning Checks
-
Ensure equipment is labeled “To Be Cleaned.”
-
Verify batch and previous product are cleared.
-
Check cleaning area is clean and free of contamination risk.
5.2 Cleaning of S.S. Bins/Containers
-
Disassemble any removable parts like lids or gaskets.
-
Rinse with purified water to remove loose material or residue.
-
Scrub using approved detergent and non-metallic brushes.
-
Rinse thoroughly with purified water until all detergent is removed.
-
Inspect for cleanliness visually.
-
Dry using clean, lint-free cloth or allow to air dry in a controlled environment.
-
Reassemble if needed and affix a “Cleaned” status label with date and initials.
-
Record cleaning activity in the cleaning logbook.
5.3 Cleaning of S.S. Pallets
-
Brush off any visible material or dust.
-
Wash with detergent and scrub all surfaces.
-
Rinse with purified water.
-
Wipe dry with a clean cloth or allow to air dry.
-
Label pallet as “Cleaned.”
5.4 Cleaning of Hosepipes and Material Transfer Pipes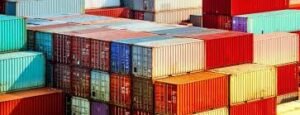
-
Disconnect hoses/pipes from equipment.
-
Flush internally with purified water to remove residues.
-
Clean externally using detergent and brushes.
-
Rinse thoroughly inside and out with purified water.
-
Hang or drain dry hoses vertically in a designated clean area.
-
Inspect for physical damage or residual material.
-
Label “Cleaned” with identification tag.
-
Record cleaning activity.
5.5 Cleaning of Accessories (Scoops, Spatulas, Funnels, etc.)
-
Wash with detergent and scrub all contact surfaces.
-
Rinse thoroughly with purified water.
-
Dry and visually inspect.
-
Label and store in a clean, designated area.
6. Precautions
-
Always wear gloves, mask, and protective clothing.
-
Use designated brushes and cleaning tools for each equipment type.
-
Avoid contamination during drying and storage.
-
Do not use damaged or unclean hoses or accessories.
-
Report any defect or abnormality to the supervisor.
7. Documentation
-
Cleaning logbook (equipment-wise)
-
Equipment label (Cleaned/To Be Cleaned)
-
Cleaning checklist (optional)
🎓 Discover one of the best Pharmaceutical Production courses available — click below to explore the course that’s shaping future Production skills.