What are the root causes of quality issues in the pharmaceutical industry.
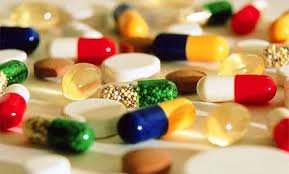
Quality issues in the pharmaceutical industry can arise from a variety of sources across the entire lifecycle of drug development, manufacturing, and distribution. Below is a detailed breakdown of the root causes:
1. Manufacturing Process Failures
-
Inadequate Process Validation: Lack of thorough validation can lead to inconsistent product quality.
-
Equipment Malfunction or Poor Maintenance: Can result in contamination, incorrect dosages, or batch inconsistencies.
-
Operator Error: Human mistakes due to insufficient training or oversight.
-
Cross-contamination: Poor segregation of manufacturing areas and materials can lead to contamination between products.
2. Poor Quality Raw Materials
-
Substandard or Adulterated Ingredients: Using low-quality or impure active pharmaceutical ingredients (APIs) or excipients.
-
Unreliable Suppliers: Sourcing from suppliers with inadequate quality control processes.
3. Inadequate Quality Control & Assurance
-
Lack of Robust Testing: Skipping or inadequately performing tests on raw materials, in-process materials, or finished products.
-
Data Integrity Issues: Falsification or manipulation of lab data to meet specifications.
-
Ineffective Quality Management Systems (QMS): Absence of a structured system to detect, report, and correct issues.
4. Regulatory Non-Compliance
-
Failure to Adhere to Good Manufacturing Practices (GMP): Non-compliance with GMP guidelines leads to increased risk of quality failures.
-
Inadequate Documentation: Missing or incomplete records of batch processing, testing, and deviations.
-
Lack of Regulatory Oversight in Some Regions: In some countries, weak enforcement results in the proliferation of substandard drugs.
5. Supply Chain Vulnerabilities
-
Improper Storage and Transportation: Exposure to heat, moisture, or other unsuitable conditions can degrade product quality.
-
Counterfeit Products: Infiltration of fake drugs in the supply chain can compromise the integrity of the pharmaceutical system.
6. R&D and Formulation Issues
-
Flawed Product Design: Poor formulation or design can cause stability issues or bioavailability problems.
-
Insufficient Stability Testing: Leads to products degrading before the end of shelf life.
7. Lack of Skilled Personnel
-
Inadequate Training: Employees unfamiliar with procedures or regulatory expectations may make errors that affect quality.
-
Shortage of Experienced Professionals: Especially in quality assurance, quality control, and regulatory affairs.
8. Financial or Ethical Pressures
-
Cost-Cutting Measures: Reducing costs at the expense of quality controls or testing.
-
Ethical Lapses: Prioritizing profits over patient safety or regulatory compliance.
9. Technology Limitations
-
Outdated Equipment or Software: Can limit the ability to detect or prevent quality issues.
-
Lack of Automation: Manual processes are more prone to error than automated systems.
Summary Table (optional format):
Root Cause Category | Specific Examples |
---|---|
Manufacturing | Inconsistent processes, cross-contamination, operator error |
Raw Materials | Low-quality APIs, unreliable suppliers |
Quality Systems | Inadequate testing, poor documentation, data manipulation |
Regulatory Issues | GMP violations, insufficient oversight |
Supply Chain | Improper storage, counterfeiting |
R&D/Formulation | Unstable formulations, inadequate testing |
Human Resources | Poor training, skills gap |
Financial/Ethical | Cost-cutting, unethical practices |
Technology | Obsolete equipment, limited automation |
🎓 Discover one of the best Quality Assurance courses available — click below to explore the course that’s shaping future QA skills.